This article is published in Aviation Week & Space Technology and is free to read until Jun 01, 2024. If you want to read more articles from this publication, please click the link to subscribe.
Turbine Blade OEMs Seek Better Durability And Efficiency

MTU is monitoring the trends in material development and will apply novel materials, such as ceramics, if they offer a good balance of improvement and maturity.
When it comes to jet engine time on wing, the maintenance status of the turbine blades lies at the heart of the matter. Engine OEMs have focused on increased durability of the blades, particularly those in the high-pressure turbine—mainly through improvements to blade materials.
“In the past, some engines have experienced maintenance challenges with [high-pressure turbine (HPT)] blade failures. These kinds of failures used to go undetected and were not usually identified until a scheduled borescope inspection,” says Brent Ostermann, vice president of product assurance and quality for StandardAero.
Ostermann explains that in recent years, the engine OEMs have moved to a “predictive mode” through considerable improvements to their engine trending software to build algorithms for detection of a potential and imminent failure. “The HPT, being the hottest part of the engine with elevated temperatures, is the area where these blade failures tend to occur,” he says. “With reccurrence of events, this poses some maintenance challenges.”
In tandem with that, Ostermann notes, the OEMs have put considerable work into designing the blades with advanced alloy materials to mitigate risk of failure. In new designs, advanced thermal barrier coatings and designs of internal cooling passages have been incorporated.
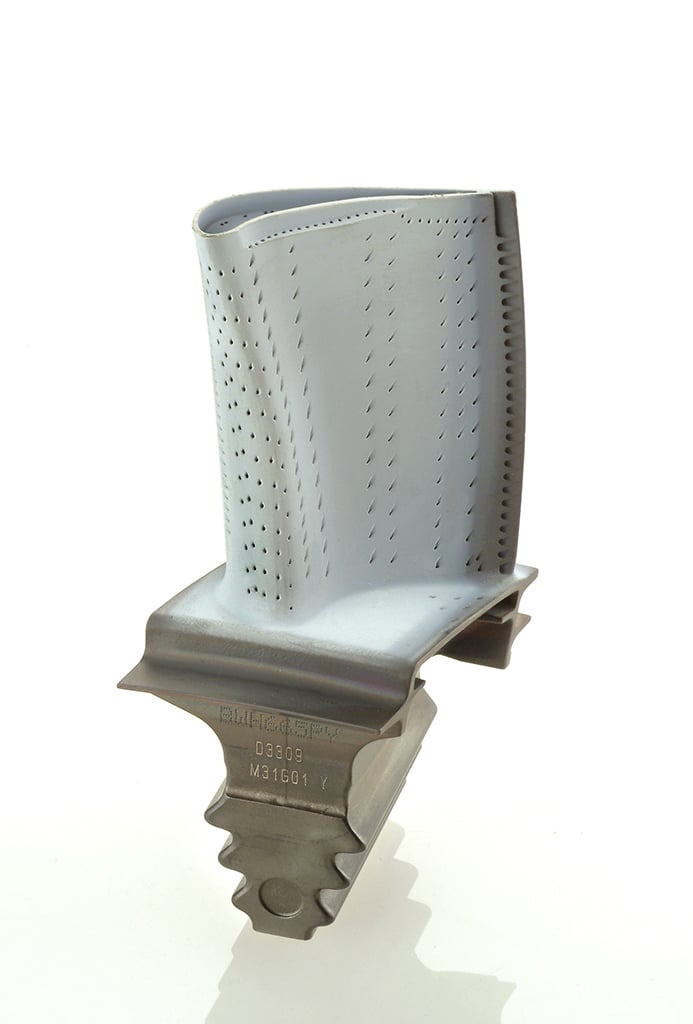
As Ostermann explains, most of the advanced alloy materials are proprietary to the engine OEMs. “Such materials are nickel-based super alloys that are single crystal, directionally solidified during the casting process for improved high thermal strength,” he says. “Advancements have also been made in recent years with thermal barrier coatings, with alumina for higher oxidation and corrosion resistance. Internal cooling also has been improved with the design of castings during the development of the blade.”
But even with design changes, some HPT blades still are exposed to extreme hot and harsh environments that subject them to failure or premature wear, Ostermann stresses. “Among the engineering goals for turbine blades is to find a solution to protect blades from the environmental conditions of a hot and harsh climate—as well as to increase time on wing,” he says.
Asked about weight savings, Ostermann reports that the newer blades are generally lighter than previous ones; however, that presents an interesting issue. “This could pose a problem dynamically, as there is potential for some system unbalance,” he says. “Some OEMs have tried to counteract this with the addition of dampers in the HPT Disk system.”
Looking ahead, Ostermann says the future of turbine blades will be a “movement into ceramics” and other materials that can withstand elevated turbine temperatures. “That is at least several years away,” he explains. “The current emphasis is on improved internal cooling designs of a turbine blade, along with more advanced materials and coatings, which will be incorporated by the next generation of jet engines. These are some of the key differences between those engines and what they will replace.”
To what degree blade improvements have contributed to greater time on wing is still to be determined, Ostermann says.
“It’s tough to attribute a number, especially with the wide variety of design improvements that have varied among the different OEMs,” he stresses. “A good target [goal] is to increase time on wing to 10,000-12,000 cycles—around a scheduled performance shop visit. More of the population of engines are making it to the scheduled shop visit without incident or premature HPT turbine blade failure.”
Redesigned turbine blades are, in fact, delivering greater time on wing. One example is the Rolls-Royce Trent 7000, which powers the Airbus A330neo family. For this engine, the OEM has developed and put into service a “durability enhancement package” featuring a new HPT blade that doubles the on-wing time, according to Caroline Day, vice president of marketing for Rolls-Royce Civil Aerospace. “We are now developing a second package of hot-section enhancements, which will deliver a future improvement of up to 30%,” she says.
Day explains that the OEM has in development its first durability enhancement package for the Trent 1000 HPT blade for the Boeing 787. This, she reports, is designed to more than double engine time on wing and is in the final stages of certification. The first phase of this package should be available in the Trent 1000 fleet starting in the fourth quarter of this year, with the second package of hot-section enhancements slated to roll out in 2026. The second package is designed to improve durability up to 30%.
“The high-pressure turbine blade improvements on both engines relate to a 40% increase in cooling airflow and a reduction of sustained operating temperatures by 45F, resulting in increased blade life,” Day says. “The shape of the blade is unchanged, but there are more cooling holes, and some have been enlarged.” Day also reports that the blades are retrofittable to the existing hardware standard.
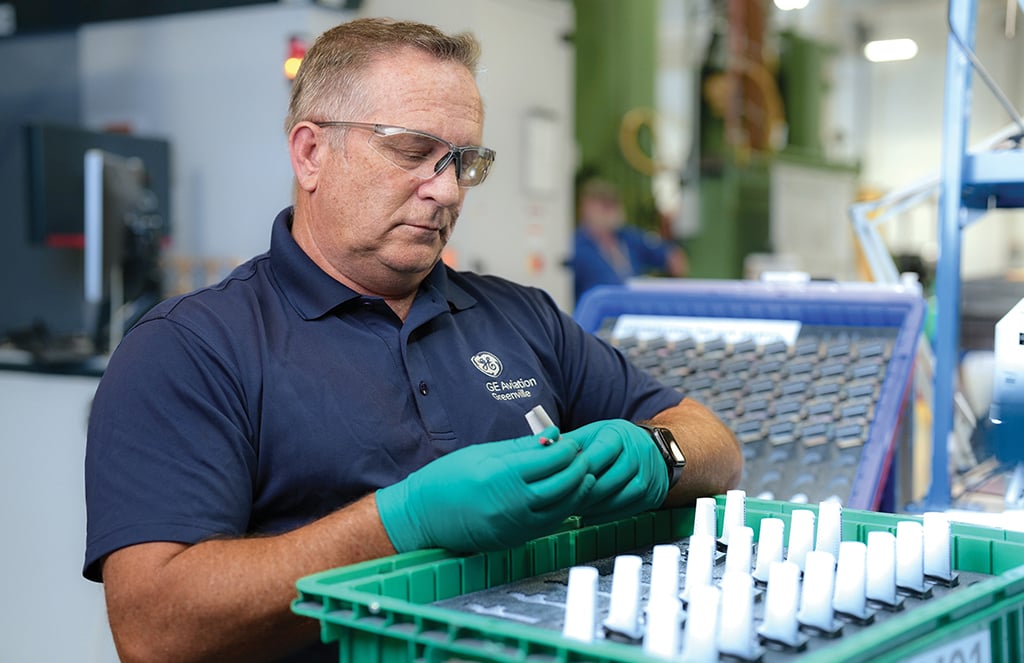
Day says Rolls-Royce also is introducing a suite of technologies to deliver an additional 1% improvement in fuel and CO2 efficiency on the Trent XWB-84, which powers the Airbus A350-900. “For the Trent XWB-97 on the Airbus A350-1000 and A350F, we are working on a series of technology packages that will improve durability and efficiency across all operations as well as doubling time on wing,” she says.
MTU Aero Engines and its partners also pushing the time on wing envelope as well, relative to current and former engine generations, according to Jens Truebenbach, the OEM’s chief engineer for advanced programs. But he points out that to achieve increased time on wing, blade design has to be adopted without sacrificing aerodynamic efficiency, in addition to material development. “MTU monitors the trends in material development and will apply novel materials if they offer a good balance of improvement and maturity,” he reports. “Ceramics are an example, and it will probably find its way in the HPT blades first.”
Truebenbach says turbine blades are especially vulnerable to foreign object damage, and in that respect, he points to the geared turbofan (GTF) concept, which features high-speed, low-pressure turbines (LPT) for minimum fuel burn.
“Because of their high circumferential speeds, these airfoils are considerably more exposed to impact damage,” he explains. “Taking this into account, we are working to get a good understanding of impact mechanisms to optimize profile shape accordingly. Furthermore, durable protective coatings are being developed and applied.”
Truebenbach notes that operations in harsh environments—hot temperatures, dust and polluted air—are the chief maintenance challenges for turbine blades in new-generation engines with high overall pressure ratios and elevated combustion temperatures. “Harsh environments are particularly challenging for the cooled airfoils in the HPT,” he says.
When asked if new metal alloys offer some promise, Truebenbach says: “Metal alloy development focuses mainly on improvement of permissible mechanical and thermal loads. Durability is secured by design.”
Interestingly, weight savings are not always a benefit of redesigned turbine blades, as Truebenbach explains using the GTF as an example.
“Turbine airfoil weight is mostly driven by aerodynamic profiling and, for a high-speed turbine, also by centrifugal load. So our GTF airfoils in the three-stage LPT are probably not lighter than those of previous generation engines,” he says. “But there are[fewer] of them, resulting in less total airfoils weight, compared to other LPTs, which have five. Next-generation turbine blades will most likely follow an evolutionary development trajectory improving aerodynamic efficiency and durability.”
Blade and vane oxidation and sulfidation, leading to thermo-mechanical fatigue, have been among the durability challenges the industry is addressing. To mitigate those challenges, new materials with super-low sulfur chemistries are being used to improve turbine blade oxidation, says Paul Woodcock, engineering director for propulsion engines at Honeywell Aerospace Technologies. Also, thermal barrier coatings (TBC) have become more prevalent to protect blades and vanes from hotter turbine conditions. New turbine blades, Woodcock says, require the use of TBCs, more sophisticated sand-tolerant cooling designs and improvements in aerodynamic features.
“Small particle erosion, particularly from sand, is a larger issue than foreign object damage,” he says. “To mitigate that, the inclusion of engine particle filtering systems is being considered for some engine applications.”
Honeywell, as with other engine OEMs, sees migration from metal to ceramics, but on nonrotating turbine parts. The advantage is higher material thermal capability and an increase in turbine efficiency from reduced blade tip clearance.
Looking ahead, Honeywell’s goals for future turbine blades include increased aerodynamic efficiency and improved airfoil cooling effectiveness, while reducing losses and maintaining a robust design to deal with extended time on wing. Advances in materials are also a key aspect of the technology road map, Woodcock says.
Tom Levin, vice president of CFM International commercial programs, also cites upcoming technological advances. He reports that an improved HPT blade is being introduced on both the CFM56-5B engines for the Airbus A320ceo family and CFM56-7B engines for the Boeing Next-Generation 737 family. “The redesign, which resulted in increased wall thickness, optimized dovetail loading and tightened manufacturing tolerances to be more durable,” Levin explains. “The blade is even more reliable than its predecessor and, compared to the prior Tech Insertion configuration, it improves time on wing as much as 25% in certain operating environments.”
In another development, Levin reports that an updated HPT blade for CFM’s Leap engine uses new casting and cooling technology to improve durability and time on wing, especially for operations in hot, dusty environments.
“The blade has shown durability improvements greater than 50% over the existing design, which will result in a time on wing equivalent to that of CFM56 in the same region,” he notes. “We’re introducing this design to the Leap 1A engines for the Airbus A320neo family and the Leap 1B engines for the Boeing 737 MAX family.”
Levin says CFM was able to validate the design of this blade with a proprietary dust ingestion rig with the capability to replicate the distress modes customers are seeing in the field.
“Working with geologists, we engineered dust that replicated the mineral content and particle size distribution observed in different regions,” Levin says. “Last year, we completed extensive testing on the Leap 1A blade, and we’re on track to introduce it to operators this year. For the Leap 1B engine, we started testing the improved design on Feb. 29—which, ironically, was also Leap Day.”